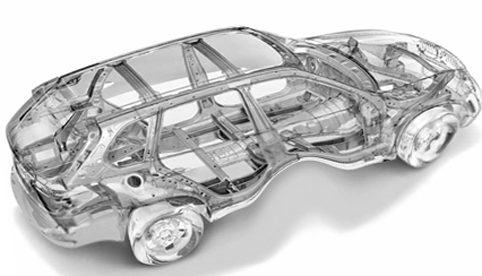
車体は何で構成されていますか?
車は多くの要素が調和して機能することで構成されています。 主なものは、エンジン、シャーシ、トランスミッションであると考えられます。 ただし、それらはすべてキャリア システムに固定されているため、相互作用が保証されます。 キャリアシステムにはさまざまなオプションがありますが、最も人気のあるのは車体です。 これは、車両のコンポーネントの固定、キャビン内の乗客と荷物の配置を確保し、移動中のすべての荷重を認識する重要な構造要素です。
目的と要件
エンジンが車の心臓と呼ばれるなら、ボディはその殻または本体です。 いずれにせよ、車の中で最も高価な要素はボディです。 その主な目的は、乗客と内部コンポーネントを環境の影響から保護し、座席やその他の要素を収容することです。
重要な構造要素として、ボディには次のような特定の要件が適用されます。
- 耐食性と耐久性。
- 比較的小さな質量。
- 必要な剛性。
- すべての車両コンポーネントの修理とメンテナンスを保証する最適な形状、荷物の積み込みの利便性。
- 乗客とドライバーに必要なレベルの快適さを提供します。
- 衝突時に一定レベルの受動的安全性を確保する。
- 最新の規格とデザインのトレンドに準拠しています。
ボディレイアウト
自動車の軸受部分は、フレームとボディで構成することも、ボディのみで構成することも、組み合わせて構成することもできます。 キャリアの機能を果たす本体をキャリアと呼びます。 最近の車ではこのタイプが主流です。
また、ボディは XNUMX つのボリュームで作成できます。
- 全XNUMX巻。
- XNUMX巻。
- XNUMX巻。
エンジンルーム、客室、ラゲッジルームを一体化したワンボリュームを実現。 このレイアウトは、乗用車 (バス、ミニバス) および多目的車両に対応します。
XNUMX ボリュームには XNUMX つのスペースゾーンがあります。 トランクとエンジンルームを組み合わせた客室。 このレイアウトにはハッチバック、ステーションワゴン、クロスオーバーが含まれます。
スリーボリュームは、客室、エンジンルーム、荷物室の XNUMX つのコンパートメントで構成されます。 セダンに似合うクラシックなレイアウトです。
さまざまなレイアウトを以下の図に示します。詳細については、ボディ タイプに関する記事を参照してください。
デバイス
レイアウトは多様ですが、車体には共通の要素があります。 それらは以下の図に示されており、次のものが含まれます。
- フロントとリアのスパー。 これらは構造的な剛性と振動減衰を提供する長方形の梁です。
- フロントシールド。 エンジンルームと客室を分離します。
- フロントラック。 また、剛性も提供し、屋根を固定します。
- 屋根
- リアスタンド。
- リアウイング。
- ラゲッジパネル。
- ミドルスタンド。 耐久性に優れた鋼板製でボディ剛性を確保。
- しきい値
- さまざまな要素(排気管、プロペラシャフトなど)が配置されている中央トンネル。 剛性も上がります。
- ベースまたは底。
- オーバーホイールニッチ。
ボディの種類(セダン、ステーションワゴン、ミニバス等)によりデザインが異なる場合がございます。 設計では、スパーやラックなどの耐荷重要素に特に注意が払われています。
硬度
剛性は、運転中の動的荷重および静的荷重に耐える車体の特性です。 コントロール性に直接影響します。
剛性が高ければ高いほど、車のハンドリングは良くなります。
剛性はボディタイプ、全体の形状、ドアの数、車のサイズ、窓によって異なります。 フロントガラスとリアウィンドウの取り付けと位置も重要な役割を果たします。 剛性を 20 ~ 40% 高めることができます。 さらなる剛性アップを図るため、各種スペーサー・アンプを装着。
最も安定しているのはハッチバック、クーペ、セダンです。 原則として、これはXNUMXつの容積のレイアウトであり、ラゲッジコンパートメントとエンジンの間に追加のパーティションがあります。 ステーションワゴン、乗用車、ミニバスのボディでは剛性不足が見られます。
剛性パラメータには曲げとねじりの XNUMX つがあります。 ねじりの場合、たとえば斜めに吊り下げて、長手方向の軸に対して反対側の点に圧力をかけて抵抗をチェックします。 すでに述べたように、現代の自動車は一体型の耐荷重ボディを備えています。 このような構造では、剛性は主に桁、横梁、縦梁によって提供されます。
製造時の材質と厚み
鋼の厚さにより構造の強度と剛性を高めることができますが、質量に影響します。 ボディは軽くて丈夫でなければなりません。 これは低炭素鋼シートの使用によって実現されます。 個々の部品はプレス加工で製作されます。 次に、部品はスポット溶接によって互いにしっかりと接続されます。
鋼の主な厚さは0,8〜2 mmです。 フレームには2~4mm厚のスチールを使用。 スパーやラックなどの最も重要な部品は鋼鉄でできており、ほとんどの場合合金でできており、厚さは 4 ~ 8 mm、大型車両では 5 ~ 12 mm です。
低炭素鋼の利点は、成形性が高いことです。 任意の形状やジオメトリのパーツを作成できます。 欠点は耐食性が低いことです。 耐食性を高めるために、鋼板には亜鉛メッキが施されるか、銅が添加されます。 塗装は腐食からも保護します。
主な荷重を負担しない最も重要でない部品は、プラスチックまたはアルミニウム合金で作られています。 これにより、構造の重量とコストが削減されます。 用途に応じた材質と強度を図に示します。
アルミボディ
現代の設計者は、剛性と強度を失わずに重量を軽減する方法を常に模索しています。 有望な材料の 2005 つはアルミニウムです。 130 年の欧州車のアルミニウム部品の質量は XNUMX kg でした。
アルミ発泡材が積極的に使用されるようになりました。 これは非常に軽量でありながら、衝突時の衝撃をよく吸収する剛性の高い素材です。 発泡構造により高い耐熱性と遮音性を実現します。 この材料の欠点はコストが高いことであり、従来の同等品よりも約 20% 高価です。 アルミニウム合金は「アウディ」や「メルセデス」などに広く使用されています。 たとえば、このような合金のおかげで、アウディ A8 ボディの質量を大幅に減らすことができました。 たったの810kgです。
アルミニウムに加えて、プラスチック材料も考慮されています。 たとえば、鋼板とほぼ同じ硬度を持つ革新的なFibropur合金。
ボディは車の最も重要な構造部品の XNUMX つです。 車両の質量、ハンドリング、安全性はこれに大きく依存します。 材料の品質と厚さは、耐久性と耐腐食性に影響します。 現代の自動車メーカーは、構造の重量を軽減するためにカーボンファイバーやアルミニウムをますます使用しています。 重要なことは、衝突時にボディが乗客とドライバーに最大限の安全を提供できることです。
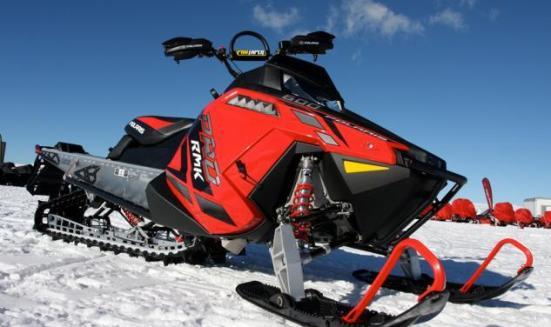
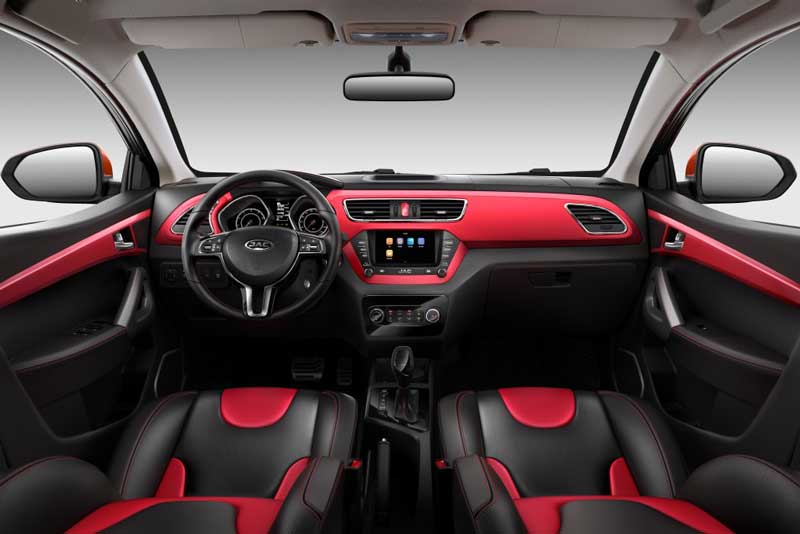