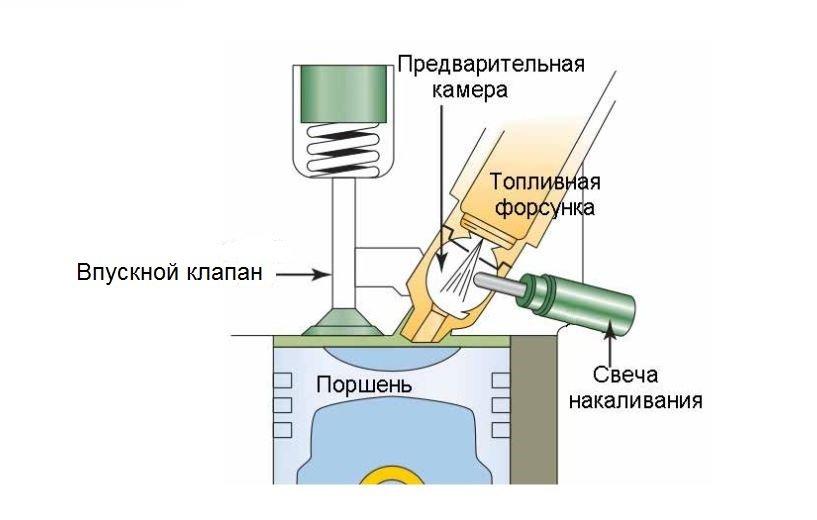
ディーゼル噴射システム。 デザイン、長所と短所
ガソリンエンジンとは異なり、ディーゼルエンジンは最初から燃料噴射がありました。 噴射システム、フィッティング、およびシリンダーに供給される燃料の圧力のみが変更されました。
一般にディーゼルエンジンとして知られているディーゼルエンジンの動作原理は、ガソリンエンジンの動作原理とは完全に異なります。 燃料トラックでは、混合気はピストンの上の燃焼室に入ります。 圧縮後、スパークプラグの電極での電気スパークの破壊により混合気が点火されます。 これが、ガソリンエンジンが火花点火(SI)エンジンとも呼ばれる理由です。
ディーゼルエンジンでは、燃焼室のピストンが空気のみを圧縮します。空気は、巨大な圧力(少なくとも40バール、したがって「高圧」という名前)の影響下で600〜800°Cの温度に加熱されます。 このような熱風に燃料を噴射すると、燃焼室内で燃料が即座に自己発火します。 このため、ディーゼル駆動列は圧縮点火(CI)エンジンとも呼ばれます。 当初から、エンジンに空気を供給するだけのインテークマニホールドではなく、燃焼室に燃料を噴射することで供給されていました。 燃焼室が分割されているかどうかに応じて、ディーゼルエンジンは間接噴射または直接噴射のパワーユニットに分割されました。
間接注入
ディーゼルは直噴システムでデビューしましたが、長く使われていませんでした。 この解決策はあまりにも多くの問題を引き起こし、自動車産業では1909年に特許を取得した間接噴射に置き換えられました。 直接噴射は、大型の固定式および船舶用エンジン、および一部のトラックに残っていました。 乗用車の設計者は、よりスムーズな操作とより少ない騒音で、間接噴射ディーゼルを好みました。
ディーゼルエンジンの「間接」という用語は、インテークマニホールドに混合気を噴射する間接噴射であるガソリンエンジンとはまったく異なるものを意味します。 間接噴射ディーゼルエンジンでは、直接噴射設計と同様に、インジェクターによって霧化された燃料も燃焼室に入ります。 燃料が注入される補助部分と主要部分のXNUMXつの部分に分かれているだけです。 燃料燃焼の主なプロセスが行われるピストンの真上のスペース。 チャンバーはチャネルまたは複数のチャネルによって相互接続されています。 形状と機能の観点から、チャンバーは予備、渦、および空気リザーバーに分けられます。
後者は生産が実質的に停止しているため、使用できません。 プレチャンバーとスワールチャンバーの場合、ノズルは補助チャンバーの隣に設置され、そこに燃料を注入します。 そこで点火が起こり、部分的に燃焼した燃料がメインチャンバーに入り、そこで燃焼します。 プレチャンバーまたはスワールチャンバーを備えたディーゼルはスムーズに作動し、軽量のクランクシステムを備えている場合があります。 それらは燃料品質に敏感ではなく、単純な設計のノズルを持っているかもしれません。 ただし、直噴ディーゼルよりも効率が悪く、燃料消費量が多く、コールドエンジンの始動に問題があります。 今日、乗用車の間接噴射ディーゼルエンジンは過去のものとなり、現在は製造されていません。 それらは、今日市場に出回っている現代の車にはめったに見られません。 それらは、インドのヒンドゥスタンとタタ、ロシアのUAZ、ブラジルで販売されている旧世代の三菱パジェロ、またはアルゼンチンで提供されているフォルクスワーゲンポロなどのデザインでのみ見つけることができます。 それらはアフターマーケット車両ではるかに大量に使用されます。
直接注入
それはすべて彼から始まりました。 ただし、直接噴射の利点は当初は活用されていませんでした。 燃料を適切に旋回させることの重要性は不明であり、その燃焼は最適ではありませんでした。 燃料の塊が形成され、それが煤の形成に寄与した。 ピストンのプロセスが速すぎて、エンジンが一生懸命働き、クランクシャフトのベアリングがすぐに破壊されました。 このため、直接噴射は中止され、間接噴射が優先されました。
ルーツへの回帰は、現代版では、フィアットクロマ1987TDが大量生産に入った1.9年にのみ発生しました。 直接燃料噴射には、効率的な噴射装置、高い噴射圧力、高品質の燃料、および非常に強力な(したがって重い)クランクセットが必要です。 ただし、コールドエンジンの高効率と簡単な始動を提供します。 直噴ディーゼルエンジンの最新のソリューションは、主に、適切な形状のチャンバー(キャビティ)を備えた完全にフラットなヘッドとピストンに基づいています。 チャンバーは、燃料の正しい乱流に責任があります。 直接噴射は、今日、乗用車のディーゼルエンジンで広く使用されています。
ダイレクトインジェクション - ポンプインジェクター
従来のディーゼルエンジンでは、さまざまなタイプのポンプが燃料の供給を担当します。 先駆的な時代には、燃料噴射は圧縮空気で行われていました。20年代には、これは再設計されたオイルポンプで行われました。 300年代には、ディーゼルエンジン用に設計された特殊なポンプがすでに広く使用されていました。 当初は、低圧(最大60バール)を生成するシリアルポンプに基づいていました。 アキシャルディストリビューター(1000バール以上)を備えたより効率的なポンプが登場したのは80年代になってからでした。 524年代半ばに、彼らは機械的噴射制御を受け、1986年代半ばには、電子制御を受けました(BMW XNUMXtd、XNUMX)。
すでに30年代にトラックで使用されていたポンプインジェクターは、燃料噴射の方法が少し異なり、1998年に初めてフォルクスワーゲンの懸念によって乗用車で広く使用されました(Passat B5 1.9TDI)。 要するに、ポンプインジェクターは、カムシャフトによって駆動される独自のポンプを備えたインジェクターです。 したがって、加圧してシリンダーに注入するプロセス全体は、シリンダーヘッドに限定されます。 システムは非常にコンパクトで、ポンプをインジェクターに接続する燃料ラインはありません。 そのため、ノズルの脈動がなく、燃料量の調整や漏れが困難になります。 ユニットインジェクターチャンバー内で燃料が部分的に気化するため、噴射タイミングが短い場合があります(始動が容易)。 ただし、最も重要なのは、2000〜2200バールの非常に高い射出圧力です。 シリンダー内の燃料の量は、空気とすばやく混合し、非常に効率的に燃焼します。
一般に、ポンプインジェクターディーゼルエンジンは、高効率、低燃料消費、高速、および高出力密度を得る可能性を特徴としています。 しかし、ユニットインジェクターエンジンは、主にシリンダーヘッドの複雑さのために、製造に費用がかかります。 彼の仕事は大変で騒々しい。 ユニットインジェクターを動力源とする場合、排出量の問題も発生し、VWがこのソリューションを放棄することに大きく貢献しました。
直噴 - コモンレール
コモンレールインジェクションシステムの最も重要な要素は、ポンプがディーゼル燃料をポンプで送る「加圧燃料アキュムレータ」としても知られているタイプのタンクである「コモンレール」です。 各シリンダーで同じ圧力を維持しながら、ポンプからではなくタンクからノズルに入ります。
比喩的に言えば、各インジェクターはポンプからの燃料の一部を待たずに、非常に高圧の燃料を持っていると言えます。 インジェクターを作動させる電気インパルスは、燃焼室に燃料を供給するのに十分です。 このようなシステムでは、多相噴射(噴射ごとに8相でも)を作成できます。これにより、圧力を徐々に上げながら燃料を非常に正確に燃焼させることができます。 非常に高い噴射圧力(1800バール)により、ほとんどミストの形で燃料を供給する非常に小さなオリフィスを備えたインジェクターを使用できます。
これらすべては、高いエンジン効率、スムーズな走行、低騒音レベル(直接噴射にもかかわらず)、優れた操縦性、低排気ガスによって補完されます。 ただし、コモンレールエンジンには、最高品質の燃料と最高のフィルターが必要です。 燃料中の汚染物質はインジェクターを破壊し、修理に非常に費用のかかる損傷を引き起こす可能性があります。
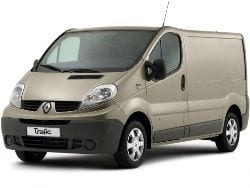
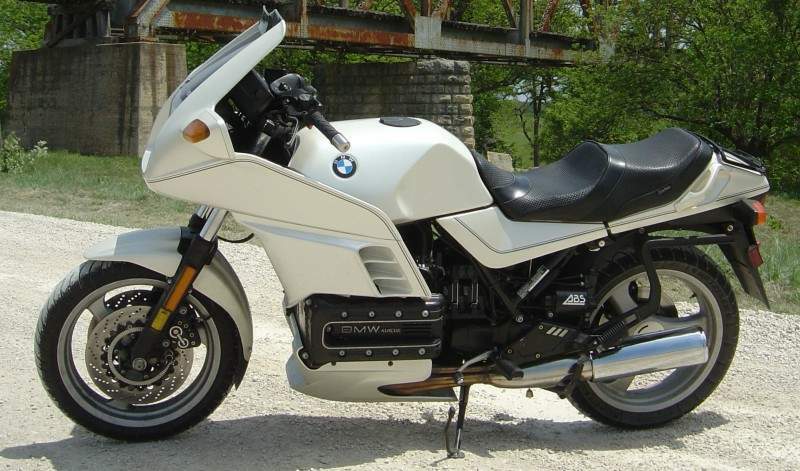